Cryogenic grinding
We manufacture complete cryogenic grinding lines, enabling efficient production of finer particles by using freezing of ground / milled material with liquid nitrogen or dry ice (solid CO2). Depending on the product properties such as strength, hardness, flexibility/plasticity and the desired particle size, the following grinding and pulverisation principles are applied: breaking, crushing, cutting, abrasion, impact.
Comprehensive work related to cryogenic grinding – from consulting on the application of technology, design of cryogenic grinding line and structural elements, to the selection of appropriate system components – is carried out in cooperation with MESSER Polska. This allows our customers to run cryogenic grinding tests in the MESSER R&D centre.
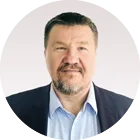
We will answer questions about: offer, technical specification, delivery, assembly.
- possibility of obtaining grains with particle sizes up to 50 µm after grinding
- grinding and pulverisation principles (breaking, crushing, cutting, abrasion, impact) are applied depending on the product properties such as strength, hardness, flexibility/plasticity and the desired particle size
- for particles smaller than 300 µm, mills with tested impact effect such as “peg mills” are suitable
Depending on the material, the following gases are used in the process:
- Nitrogen (liquefied)
- or CO2 (liquefied)
Cryogenic technology is used to grind/pulverise:
- food products and plant materials: herbs, spices, beans (e.g. coffee), dried fruit, etc.
- plastics, polymers, rubber,
- wax, paraffin wax, resins, paint pigments, etc.
Cryogenic grinding is applicable in:
- pharmaceutical industry
- rubber industry
- plastics industry
- food industry
- production of industrial mills
- recycling
- higher efficiency of the production process
- possibility of obtaining finer powders
- no thermal damage (e.g. when grinding pharmaceuticals)
- no oxidation damage (e.g. when grinding nuts)
- no evaporation of aromatic oils (e.g. when grinding spices)
- no fire or dust explosion hazard
- no clogging or blocking of the grinding elements
- consulting on the application of cryogenic grinding technology
- cryogenic grinding line design
- selection of system components
- design and supply of structural elements
- supply of the mill, cooling system, separators, dust extraction system, transport systems, final product receiving system and packing line